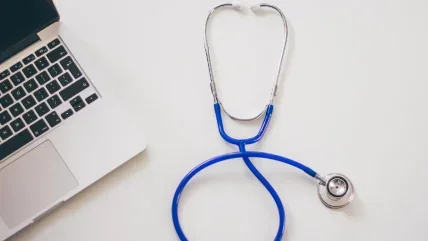
The term ‘Industrie 4.0’ was coined by the German federal government in a national strategy to promote the computerisation of manufacturing in 2011. It was subsequently established in the US, Japan and China, all of which adopted their own plans for the revolution.
Industry 4.0 comprises of four key elements: the internet of things (IoT), internet of services (IoS), cyber-physical systems (CPS) and the smart factory. IoT consists of a ‘network of physical objects’, where the radio-frequency identification (RFID), wireless sensor networks (WSN), and middleware and cloud computing are the most common technologies employed.
Based on the technologies of IoT and a close loop of sensors, actuators and other devices, the CPS integrates physical and cyber networks, providing more intelligent, transparent and efficient methods for information exchange inside and outside the company. These technologies help companies achieve more robust, closer and flexible linkages in manufacturing, which optimises value chains, cost reduction and energy saving.
Slow on the uptake
Despite their huge potential for improving transparency, quality, safety and efficiency in manufacturing processes, the complex and stringent regulatory environment has meant that the pharma industry has been slow to adopt industry 4.0 technologies.
The majority of manufacturers still use batch-based mass production processes rather than continuous production. The lack of robust on-line quality control and flexible production act as a bottleneck of reliable drug supplies and, therefore, shortages occur routinely.
There are other benefits to adopting continuous manufacturing methods. Traditional batch production has considerable impact on the environment, in terms of air emissions, chemical pollution, waste water and residual waste. In contrast, continuous production methods have lower raw material consumption and require fewer hazardous solvents.
Through greater use of process analytical technology, real-time data processing, 3D printing, robots and other techniques comprising industry 4.0, continual processing can be achieved, reducing the industry’s carbon footprint and improving its energy efficiency and solvent utilisation, while enhancing the quality and control of the entire system.
In light of the ongoing developments in genomics, combined with the increase in chronic diseases worldwide, the demand for patient-centred treatments is growing. The enhanced productivity of industry 4.0 technologies can enable personalised medicines to be created more easily.
It is not just manufacturers that can gain value from adopting industry 4.0 technologies. Distributors, healthcare providers and pharmacies could all benefit from the implementation of auto-ID tags, smart vehicles, patient-centric information exchanges, cloud computing and big data analytics.
Change for the better
Modern information and communication technologies like cyber-physical systems, big data analytics and cloud computing can all help with the early detection of defects and production failures, enabling them to be prevented. Productivity, quality and agility can all be increased, providing significant competitive value. Greater use of cloud technology does carry certain risks, however, particularly with regard to security.
Just-in-time manufacturing can be integrated into production, reducing the waste created by high levels of safety stocks and facilitating the production of personalised products on small batches by upstream suppliers.
The new energy management techniques supported by industry 4.0 can also monitor and optimise energy consumption via automotive sensors. In developing countries, most pharma companies have already begun to implement these kind of processes on an individual production machine level. Insights from big data on energy and cost will enable these to be scaled up to multiple production lines.
Traditional manual data records can be gradually replaced by automation systems, improving the standard and quality of data collections. Embedded sensors not only collect relevant data with regard to production processes, but can also record the environmental data, allowing real-time monitoring and traceability along the production line. The sensors then upload all data to the cloud computer for it to be stored, traced and analysed. This makes it easy to comply with good manufacturing practice as electronic records avoid the risks involved of relying on paper-based records.
Greater implementation of industry 4.0 technologies also help to avoid the large gap between scaling-up and commercial production, allowing drug breakthroughs to be quickly brought to market.
The continuous manufacturing process can also shorten the pharma supply chain, potentially shifting centralised manufacturing into regional decentralised production processes. The flexibility of this method also enables products to be more easily adapted for countries with differing regulations, where the dose, specification, packaging unit or quality test requirements may all need to be adjusted.
3D printing is an essential element of continuous production as the technique allows for rapid and personalised products to be created. This form of on-demand production is particularly valuable in improving the accessibility of drugs in resource-limited settings. 3D printing can also provide new possibilities in terms of dosage and the shape of drugs, facilitating more complex drug release profiles that can reduce side effects and boost drug adherence.
Industry 4.0 technologies can also create much more accurate supply chain data, allowing for better predictions to be made. For example, analysing historical data can help to select a potential supplier, monitor their current performance and establish best practices going forward.
The high amount of regulation in the pharma industry provides additional barriers but also means that there is huge value to be gained from digitisation. Every aspect of a pharmaceutical product’s development, testing, manufacturing, packaging, marketing, storage, distribution and use can be scrutinised, and data can be captured, analysed and reported at every stage.
Pharma companies often adopt continuous process verification (CPV), where all data generated during product manufacturing is continuously assessed and validated against regulatory guidelines, to ensure they stay within specified parameters. Hundreds, sometimes thousands, of variables need to be monitored to determine whether they fall within the specifications established for this process, which is ideally suited for industry 4.0 technology.
There are several ways that industry 4.0 technologies can contribute to CPV. One of these is through analytics. Statistical process control techniques can be used to create the data collection plan, and the statistical methods and procedures can be used to measure process stability and capability.
A risk-based real-time approach can be adopted, verifying that a process is producing material that meets all critical quality attributes and control strategy requirements. In-line, on-line or at-line controls can also be implemented to monitor process performance and product quality. In addition, quality attributes of incoming materials, in-process materials and finished products can be conducted.
Consider the potential
Everything is becoming more digitised, which provides a wealth of benefits: improved efficiency and quality, and an enhanced ability to achieve compliance with complex and ever-increasing regulation. There is now a wealth of technologies to choose from and it is imperative for companies to consider what one provides the largest benefits to their organisation.
The potential of industry 4.0 is clear and many companies are rushing to adopt it, without clarifying the key problems they face and exactly how the technologies will solve them. Key stakeholders need to consider the organisation’s culture and how to help employees at all levels adjust. This requires tackling the human tendency to resist change, as well as providing adequate training to employees. In some cases, people’s roles will change but there is also the potential that some redundancies will occur.
Adopting pharma 4.0 involves considerable commitment and resource allocation by the IT department to ensure that necessary connections are created and maintained. This also helps to avoid any issues that might cause expensive production outages.
There is also a number of questions and problems that need to be considered. For example, some software technologies require moving and/or duplicating historical data. This creates its own set of issues, both in terms of external data security and internal validation of the data. It is important to determine whether a validated database needs to be duplicated, for example.
Such decisions demand considerable time and resources, all of which need to be factored into industry 4.0 adoption processes. The economic benefits of adopting these technologies also need to be calculated and an expected return on investment for each stage should be estimated.
A well-thought-out process to implementation is key. There needs to be a clear step-by-step plan, detailing what problems need solving most urgently, who and what needs to be involved in solving them, and finally a pilot project with the technologies that are intended to be used.
2011
Year the term ‘Industrie 4.0’ was coined by the German federal government in a national strategy to promote the computerization of manufacturing.
The ‘social supers’
Leaders claim that societal impact is an organisational priority, but many still struggle with the tension between positive impact and profits. Has anyone cracked the code? The data was examined to identify leaders who seem to have figured out how to ‘do well by doing good’ by generating new revenue streams through socially or environmentally conscious products or services and believe that societal initiatives, more often than not, contribute to profitability.
These social supers consider social initiatives fundamental to their business models in the age of industry 4.0. They see social initiatives as integral to organisational health and translate their optimism about ‘doing good’ into confidence across a variety of areas.
An appetite for disruption
Social supers appear more likely to invest in new technologies than others to disrupt the market (42% versus 29% of everyone else) and feel ready to lead their organisations in capitalising on the opportunities associated with industry 4.0 (39% versus 31%).
An able, proactively trained workforce and an ethical mindset
These leaders were also more likely to declare their workforce composition prepared for industry 4.0 (44% versus 3%) and demonstrate a far greater willingness to train their workers (54% versus 37%). Furthermore, they reported deeper concern with the ethical use of industry 4.0 technologies (39% versus 26%), though they consider ethics less of a challenge as they seek to invest in industry 4.0 technology. This is likely because they’re already keeping these considerations at the top of their mind.
More holistic and defined decision-making processes
Social supers exhibit greater rigour around decision-making, reporting more clearly defined decision-making processes, a greater propensity to use data-driven insights in decision-making, and a preference for seeking input from diverse and inclusive sets of stakeholders. While it may be a leap to suggest organisations that prioritise social responsibility are better run, better prepared or more successful, evidence clearly shows that many well-run companies are guided by leaders who see the connection.
Source: Deloitt