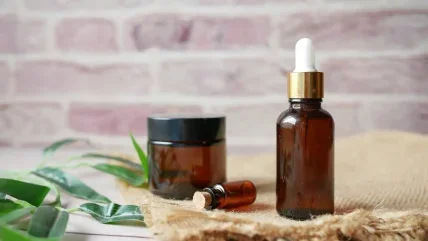
Packaging may not be the aspect of pharmaceutical development that receives the most attention, but the choices manufacturers make about how their formulation is stored, presented and delivered to the patient are just as important as the combination of active ingredients and excipients. If the primary packaging isn’t compatible with the pharmaceutical or delivery device or if it isn’t sterilised or stored correctly, the hygiene, safety and functionality of the drug can all be compromised.
Glass has been the most popular primary packaging mode for pharmaceutical manufacturers for decades, or perhaps more accurately centuries. Apothecaries didn’t have access to affordable plastic containers, but they could avail themselves of the many benefits of glass as a packaging material. Its low permeability means most formulations can be stored safely and protected from elements such as microorganisms, oxygen and water, which could degrade the product and cause safety issues. In addition, unlike plastic materials, which contain various components that can migrate from the primary packaging into the product, leaching-related incompatibility is rarely an issue with glass. “The components that come from glass are typically alkaline earth metals including sodium, calcium and barium, which are generally not of any concern from a safety perspective,” explains Hanns-Christian Mahler, chief enablement officer at ten23 health, which supports pharma and biotech clients in developing, commercialising and optimising their sterile drug products.
Mahler previously held senior roles at Lonza, Roche and Merck and has published more than 120 manuscripts and co-invented more than 50 patents, many around primary packaging. “There will always be a formulation where there is not great compatibility with glass, for example if someone chooses a sulphate buffer,” he says. “But unless you make the wrong choices in your development, glass is typically the most compatible, protective and established primary packaging of choice.”
That’s not to say there aren’t any drawbacks, or exceptions. Glass is a fragile material, something that can be mitigated by secondary packaging. It’s also more difficult to produce glass with very tight dimensional control, a factor that must be carefully considered when the primary packaging needs to be integrated with a drug delivery device.
“Glass compounds in primary packaging will be more variable in their dimensions compared to any plastic, so if you have a glass syringe that needs to be combined with a plastic device, the plastic device must be well-designed to compensate for the imprecision that you have with the glass,” Mahler explains. “For this reason, every device manufacturer loves plastic materials on the primary packaging side because it makes the integration easier and a better fit.”
With certain formulations – and when glass is exposed to significant heat during terminal sterilisation – delamination can also occur. “This is where the inner surface of the glass container is attacked by the formulation and glass particles might get into the product solution over time and make it non-compliant,” Mahler says.
The silicone that is required to lubricate glass syringes is also incompatible with a small number of pharmaceutical formulations, although Mahler believes it has received excessive negative attention. Nonetheless, a number of companies are now considering changing their primary containers from glass to plastic for these formulations, so they have lubricant choices other than silicone.
Integrated thinking
A believer in integrated design and holistic thinking, Mahler advises manufacturers to choose the packaging and the formulation of a drug at the same time. “It could be a chicken and egg discussion – do we choose the container because of the formulation or the formulation because of the container,” he says. “But what we do is develop a product from an integrated, design-thinking perspective, developing the formulation and choosing the appropriate primary packaging simultaneously.”
After ascertaining what the right container is from a product stability and quality perspective, there are many other parameters to be assessed. This can be as simple as finding a company that can supply the product reliably, in accordance with Good Manufacturing Practices (GMP), and ensuring the production process is reproducible.
“Nowadays, with the pandemic making things a little volatile and uncertain, you might want to have a back-up for raw materials, including primary packaging,” Mahler adds. “Do you have the choice of a second source with comparable quality or even identical packaging?” Sponsors also need to think about whether the primary packaging fits the manufacturing facilities they have – or have access to via a CDMO. “You have to make sure that you have a manufacturing option for the primary packaging that you’re choosing and that it’s not just wishful thinking,” he stresses. “I’ve come across innovators who have interesting approaches from a stability perspective but these containers would be very difficult to be filled. It’s great if you have a fantastic product but if you cannot produce it, you cannot industrialise it.”
In addition, all the components of the packaging need to be considered at the very beginning of the development process. “As an example, if you’re choosing a glass vial, it’s important to make the choice as a system. You need to choose a vial, rubber stopper and crimp cap in connection to your production process and your formulation considerations. It really comes back to integrated product design,” Mahler says. “It doesn’t help if you choose a vial and later choose a stopper then maybe the stopper doesn’t fit. The system won’t show sufficient closure integrity.”
Shelf-life and sterilization
Shelf-life is another important point for manufacturers to consider. If glass precipitation occurs due to a reaction with an incompatible formulation, it could take 18 months after filling for this to be detected during stability testing. Similarly, an injector device could stall years down the line if the primary packaging includes too little silicone lubricant due to concerns about using too much. “You could observe stability issues, usability issues, manufacturing issues or container closure integrity issues, which would touch the heart and soul of a sterile product,” Mahler says. “Primary packaging choice must be made with the end in mind. If you’re targeting a product that should be used with an injector and you’re targeting a five year shelf life, that’s the design that you must have in mind and that's the trajectory of the product design you need to make.”
Sterilisation procedures can also have a significant impact on glass containers. “If there’s still some remaining water from the washing process in the glass and you heat it up to 250oC, water can be a pretty nasty and aggressive solvent. So it’s very important to decide on what processing you have in your internal facility versus any ready-to- use primary packaging, paying close attention to particulates, endotoxins and any other contaminants,” Mahler says.
It always comes back to the fact that packaging should not be the choice of one department, whether that’s procurement, formulation or manufacturing. “You really have all these to take into account,” Mahler stresses. “Choice of primary packaging is not to be taken lightly. You can’t simply be inspired by a vendor and say, ‘That sounds great, I’m going to try it’. At the end of the day, you really have to make a wise choice because the failure modes are many.”
Expanding understanding
Two of the most exciting areas of research in the primary packaging field are coatings and surface treatments, which are being developed to overcome some of the traditional downsides of plastic and polymer containers, and studies into new and improved methods of closing and sealing glass and plastic containers.
“As more complex primary packaging comes forward, the question of container closure integrity becomes a more difficult one to answer,” Mahler says. “System thinking is one of my favourite terms and again it goes back to thinking about the container closure system at the outset and how you want to qualify that on a container closure endpoint.”
The scientific community’s understanding of newer and more sensitive biologic drugs and how they interact with various forms of packaging also continues to evolve, something Mahler is convinced will accelerate in the next ten years.
“It’s difficult to say which areas will be the next level of where you want to dig deeper, but there are big questions to answer around novel containers and coatings, as well as a lot of opportunities for further studying the interaction with processing formulations and primary packaging,” he concludes.