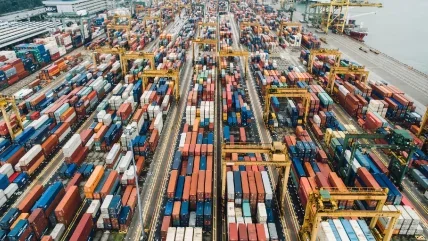
During the pandemic, everything changed. And nowhere was this more the case than in the pharmaceutical sector, which found itself having to develop and ship new products around the world with an unprecedented urgency. In non-pandemic times, far more pharmaceutical products are transported by sea than by air – 3.5m tonnes against 0.5m tonnes, according to the Seabury Group.
The main reason for this is cost: transporting a product by air is 10–15 times more expensive than transporting it by sea. Using sea freight also makes sense if you are transporting goods in bulk. There is far more capacity in a ship than in a passenger plane – the preferred option for about 70% of pharma goods sent by air. If you want to send large quantities of a generic product from, say, the US to Europe, then sea freight makes perfect sense.
There are exceptions, of course. If you have a new product, as Erik Agterhuis, an ATP biotech supply chain expert, points out, “the sooner it is on the market the better”. The likelihood is that you will be transporting small volumes, so it is worth the investment of paying a hefty sum to send it by air. In other words, says Agterhuis, “higher value, lower volume” goods go by air, while “higher volume, lower price” goods go by sea.
Shelf life
Another consideration is shelf life. “When you have a one-week shelf life for a fresh product, or maybe even two months, it’s always air,” says Agterhuis. Some products, such as drugs for clinical trials, need to be delivered quickly. Agterhuis cites an example from his last job, which involved shipping a CAR T cell therapy. With this particular class of product, blood has to be taken from the patient, transported to a manufacturing site for processing, and then returned quickly so that it can be transfused into the patient, where the CAR T cells attack the cancer cells. In situations such as these, air transport is the only option.
During the pandemic, however, other considerations came into play. Covid vaccines and drugs, along with personal protective equipment (PPE), needed to reach their destination quickly. Sending them by ship – a journey that might take weeks or even months – was not an option. But with the grounding of so many passenger flights, air transport became challenging. As pharma companies began switching from sea to air, many airlines made the decision to convert some passenger planes to freighters (or “preighters”, as they became known). The increased demand, combined with reduced availability, meant the cost of air freight rose almost three-fold.
It wasn’t always easy. Special arrangements had to be made for transporting the Pfizer vaccine, which in the early days had to be kept at -70 degrees Celsius, far below the usual cold chain requirements. Pfizer developed cold containers that could keep the vaccine at the right temperature for up to 10 days, using remote GPS capability to monitor the temperature. Exempting United Airlines from the normal limitations on dry ice, the Federal Aviation Administration (FAA) gave permission for 15,000 pounds of the phase change material to be transported on each flight to keep the vaccine supplies cold.
Sea freight costs
At the same time, there were challenges with sea freight, including a shortage of TEU (twenty-foot equivalent unit) containers used to ship goods. Worldwide, there are 17m TEUs, with 6m routinely transporting freight, frequently between China and other countries. But during the pandemic, China drastically cut exports of retail goods, meaning that TEUs brought to China stayed there, creating a shortage worldwide and helping to push up the cost of sea freight tenfold. The lack of containers “kicked back many of the shipments to air freight, because it’s way more flexible,” says Manuel Zollondz, an independent supply chain consultant. The other consequence was that for a short period, air freight was only three-to-five times more expensive than sea freight, adding to its appeal.
Now the pandemic is over, however, the price differential is returning to pre-pandemic levels, and the drivers for using air freight are less compelling. One of the factors that makes sea freight attractive is the growing importance of carbon emission targets, with pharma companies required, by 2025, to reduce emissions intensity by 59% from 2015 levels. Zollondz says that, in his experience, about 80–90% of tenders from pharmaceutical companies include a section on carbon footprint.
“You do one part of the shipment, for example from Asia to the Middle East, by ocean, and then they have big cargo airports close to the port, and they convert it for the last mile to air freight.”
Manuel Zollondz
From this perspective, sea freight wins handsdown: aeroplanes have a carbon footprint 20-30 times higher than that of ships – although some airlines are moving to sustainable aviation fuels (SAFs), which are estimated to reduce carbon footprint by up to 80%. There is an argument, too, that ships emit pollutants into the sea, contributing to ocean acidification. Nonetheless, AstraZeneca is now moving up to 64% of its volume to sea transport, while both Eli Lilly and Merck & Co have announced plans to switch from air to sea freight. Earlier this year, specialty pharmaceutical company Pharmanovia said it would divert 75% of its air shipments to sea by the end of 2028.
Cold chain challenges
Making the switch from air to sea involves careful planning; as Agterhuis points out, it requires making sure that the receiving country is able to build up stocks of product, because of the longer time period before new stock arrives – more stock, he notes, creates more risk. One project he worked on, which involved switching from air freight to sea freight for transporting products from Europe to New Zealand, took between six and nine months to implement.
The complicating factor in all this, however, is the cold chain problem. The EU’s Good Distribution Practice (GDP) guidelines, introduced in 2013, state that the storage temperature detailed on the product label by the pharmaceutical manufacturer must be maintained during transportation, adding to the costs. In products such as vaccines or biologics, maintaining control of the cold chain at every stage of the transportation is essential. This is particularly important at points of transition, notes Wim van der Schouw, a senior logistics consultant with a background working in pharmaceutical cold chain transportation. “In harbours where they change road freight into sea freight or sea freight into road freight, these terminals must be controlled very stringently,” he explains. Indeed, cold chain breaches account for about 20% of the damage that occurs to temperature-sensitive products in transit.
Traditionally, the safer option for maintaining the cold chain is to transport the goods by air, because the journey is so much shorter. Having to keep a product at the required temperature for hours is easier than keeping it at that temperature for weeks or months. There are, however, those who argue that there are often more disruptions by air, caused by poor weather, customs problems or the misloading of cargo – leading to more temperature excursions. Some pharma companies that use air freight have moved from passive packaging solutions (such as dry ice or gel packs, combined with thermal blankets for insulation) to active – but more expensive – solutions such as Envirotainers, which use electrical cooling systems that can adjust for ambient temperatures.
It’s also the case that the storage technology used in sea freight has improved greatly in recent years. Temperature-controlled reefers have backup systems in case of failure, while satellite technology enables the temperature to be monitored remotely, sending out alerts if a deviation in temperature is observed. This means that for pharma companies who want a low-cost, environmentally friendly solution, the cold chain requirements are no longer necessarily a barrier to using sea freight.
Mix and match
Some companies, says Zollondz, have chosen to maximise efficiency while minimising carbon footprint by combining air and sea – an approach known as intermodal transport: “You do one part of the shipment, for example from Asia to the Middle East, by ocean, and then they have big cargo airports close to the port, and they convert it for the last mile to air freight.”
Road transport is often used to transport pharma products between European countries, and is less risky than either sea or air, van der Schouw points out: “There are always terminals [in sea and air transport] that don’t manage the GDP guidelines as stringently as they should.”
While in some cases, the decision to use sea or air is black-and-white – sea for low-value mass market products with a long shelf life, and air for new, high-value products shipped in small quantities – there is a large grey area in the middle where the decision is not clear-cut. Considerations such as cost, cold chain requirements and environmental targets all play their part, and technology is developing at a pace that closes a gap that once seemed wide.