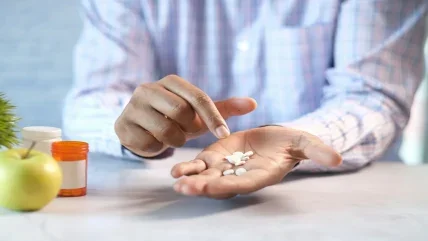
With such a wide selection of contract manufacturers in the pharmaceutical market, choosing one to partner with may seem like a simple decision. But this common misconception can lead to the activity being rushed and mistakes being made.
Larger pharmaceutical companies have departments consisting of outsourcing specialists, while smaller companies tend to have to rely on their own instinct. In either case, it’s important that companies carefully evaluate the options for compatibility with their products and quality standards.
Lloyd Mager, market solutions officer for Trust.med, explains that there’s some key factors that pharmaceutical companies should be taking into consideration when deciding on a contract manufacturer to partner with. “Manufacturers look at capability to properly package the product, and that includes the ability to apply unit level serialised data carriers,” he says.
The key factors
The increasing threat of counterfeit drugs is placing a huge burden on the pharmaceutical industry, and the assignment of a unique serial number to each product on the market is an important preventative measure. According to data published earlier in the year from the Pharmaceutical Security Institute, nearly 6,000 pharmaceutical crime incidents were reported to the organisation in 2021 – 38% more than the year before and the highest figure in almost 20 years. In low- and middle-income countries, the counterfeit threat is even greater, with the WHO estimating 10% of medical products circulating in these regions are counterfeit.
“One key process that is critical for drug processes is the ability to aggregate units to cases accurately, creating serialised relationships in the packaging,” explains Mager. Many regulations, such as the Drug Supply Chain Security Act (DSCSA) in the United States and the Falsified Medicines Directive (FMD) in the European Union, mandate accurate serialisation and aggregation to enhance patient safety and combat counterfeit drugs.
Of course, serialisation is just one of many ways to combat this issue, but it remains a crucial factor to consider when picking the right manufacturing partner. For Viraj Gandhi, CEO at Medivant Healthcare, one of preeminent concerns should always relate to the end result of the manufacturing process – the quality of the drug. “Quality control and assurance are paramount when drug companies are evaluating contract manufactures,” Gandhi says.
Given that its end users are patients, maintaining the highest quality standards is paramount in the pharmaceutical industry. Contract manufacturers must have robust quality control systems in place to ensure consistency and safety in their products. Cost efficiency also needs to be at the forefront when making the decision, however, it’s essential to strike the balance between this and product quality.
As well as cost, geographical location plays a crucial role in the decision-making process. The choice between local and international manufacturers can affect logistics, supply chain efficiency, and the ability to manage and oversee production. If a company does decide to go with an overseas manufacturer, they need to weigh the pros and cons before making an informed decision. Other key factors that play an important role include capacity, communication, and suitability with product areas. Many pharmaceutical companies also place an emphasis on the environmental impact of their operations and how contract manufactures are able to address this.
Reputation matters
In the wake of the Covid-19 pandemic, reliance on contract manufacturing has increased significantly, which has highlighted several flaws in their systems. As such, checking the reputation of the manufacturer has become a crucial part of the process. “In particular, the ability for a packaging organisation to produce compliant products for each market is critical,” Mager says. “Drug shortages have occurred due to package operations failures.”
A study conducted by the University of Utah Drug Information Service found that ongoing and active drug shortages are at the highest they’ve been in a decade. While this may not be entirely due to operations failures, ensuring that you’ve partnered with a reputable contract manufacturer is one simple step companies can take to guarantee their product meets demand.
“Maintaining proper controls and documentation for all materials, equipment, and processes provides critical assurance of quality standards.”
Viraj Gandhi
Other potential issues that could arise by choosing a partner with a poor reputation include the potential for recalls and patient safety being put at risk. One way to find out the reputation of a manufacturer is by assessing their compliance with current Good Manufacturing Practices (GMP) regulations, a baseline requirement for contract manufacturers.
A lot of the time, quality control is a built-in part of the manufacturing process. But ensuring a manufacturer complies with GMP is a critical step to protecting the reputation of a pharmaceutical company and its products.
“Companies will audit facilities, examine training records, and review manufacturing back records to verify GMP adherence,” says Gandhi. “Maintaining proper controls and documentation for all materials, equipment, and processes provides critical assurance of quality standards.”
Another major flaw highlighted by the Covid-19 pandemic was the vulnerabilities in global supply chains. However, since the height of the pandemic, contract manufacturers and pharmaceutical companies have re-evaluated how best to mitigate these risks. “This includes identifying alternate supplies and balancing cost with quality assurances,” says Gandhi. “The pandemic has really highlighted the importance of contractual terms, transparency, and relationships with strategic partners.”
Industry trends
Pharmaceutical companies are beginning to seek out more collaborative and strategic partnerships with contract manufacturers, and this is no surprise when estimates suggest between half and two thirds of pharmaceutical manufacturing is outsourced. The trend is also reflected in the contract manufacturing market, where companies have been investing heavily in their capabilities not just to manufacture drugs, but to play a role in their development too.
This shift from working with contract manufacturers to working with contract, development and manufacturing organisations (CDMOs) not only allows for improved relationships, but also better long-term strategies. One major benefit is that pharmaceutical companies can put the money they save through outsourcing development into commercialising products once they reach the approval stage.
It’s not just development capabilities that contract manufacturers (or CDMOs) are investing in either. The fourth industrial revolution is changing the way their manufacturing process operates too. “There is an increasing focus on innovation and technology to improve quality, efficiency, and transparency in contract manufacturing,” Gandhi explains. “Advanced monitoring systems, data analytics, and automation can prevent errors, reduce variability, and provide greater visibility across the end-to-end manufacturing process. Factories of the future leverage these digital capabilities alongside smart facility design.”
In particular, the adoption of advanced manufacturing technologies is one of the most significant trends in the sector. The most ambitious goal in this trend is the focus on continuous manufacturing – where pharmaceutical products are produced using a flow approach, without any interruptions. This end-to-end approach is gaining traction due to its ability to produce more consistent quality, shorten production times and allow for better resource allocation.
Even without reaching the level of continuous manufacturing, the industry is making better use of artificial intelligence and robotics, both of which are becoming more prevalent due to their ability not only to streamline the manufacturing process, but also improve quality control and efficiency. While these advancements come with criticism due to reduced need for manual labour, the product consistency and quality standards speak for themselves.
Of course, there are also trends outside the realm of technology having an impact on manufacturing. As we slowly enter the era of personalised medicine, the development of therapies tailored to individual patient profiles may become more prominent. Contract manufacturers can accommodate this move by introducing more flexible processes that focus on small-batch production and customisation.
Small-batch production not only aligns with personalised medicine, but also contributes to reducing waste and improving sustainability. By producing only what is needed, pharmaceutical companies can minimise excess inventory, ultimately benefiting both the environment and their bottom line.
It’s clear that pharmaceutical contract manufacturing is undergoing a transformative phase in an attempt to become more efficient and sustainable, while adapting to the evolving needs of pharmaceutical companies. The core considerations of quality, compliance and reliability will continue to drive decisions about the outsourcing partners companies will use to manufacture their products. But with the benefits of the fourth industrial revolution becoming more tangible, demonstrating the value of new technologies could be the key to long-term relationships with pharmaceutical clients.
As contract manufacturers evolve their production processes and look to add services to respond to the shifting priorities of the pharmaceutical market, staying informed about these trends will be essential for companies aiming to maintain a competitive edge and effectively navigate the shifting landscape.