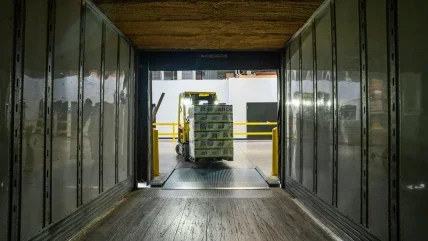
Pharmaceutical supply chains have become global and more complex, with outsourcing to contract manufacturers an increasingly large component, and new delivery and logistics methods reshaping how they operate. As these changes manifest, it is critical to ensure that supply chains can withstand shocks, and the Covid-19 pandemic has provided the ultimate test.
According to management consultancy McKinsey & Company, the worldwide value of pharmaceutical goods has grown sixfold in the past two decades, rising from $113bn in 2000 to $629bn in 2019. They’re also delivered through much more complex and opaque supply chains, with research showing for some products that supply chains start in Asia and circumnavigate the globe twice. Faced with a global pandemic, the need for accelerated vaccine development and rollout, and all of the usual demands unrelated to Covid-19, the pharmaceutical supply chain has been under unprecedented pressure. Nevertheless, while there have been some shortages of key ingredients, they have held up well.
“Supply chain risks are unavoidable,” remarks Tacy Foster, partner at McKinsey and an expert in pharmaceuticals and medical products manufacturing. “In fact, research from McKinsey Global Institute shows that supply chain disruptions are increasing in frequency and severity, with a significant shock occurring every 3.7 years on average. Companies can minimise their disruptive effects by building supply chain resilience through greater visibility, rigorous risk management, and advanced technologies.”
“Leading pharma companies have succeeded in adapting their supply chains to drive growth and manage costs,” she adds. “To do that, however, they must first start by assessing what type of risks their supply chains are exposed to, and implement plans so they can adapt quickly in the event of a disruption, be it cybersecurity risks, severe weather events or geo-political shifts.”
Remapping the world
During the pandemic, major concerns were raised about the impact of Covid-19 on China and India, both of which have become vital to the global supply chain.
“The supply chain has held up well, though there have been different stages of concern,” says Rory Horner, senior lecturer at the University of Manchester’s Global Development Institute. “It was initially seen as a China problem in early 2020, because many APIs and other ingredients are produced there. There was a fear of China’s production shutting down but, in fact, it kept going.”
“In India, a lot of companies had production shortfalls in early 2020, but the government gave pharma companies exemptions from lockdowns so they could keep producing,” he adds. “The fear that key production locations would shut down did not materialise, so the reason for shortages of some key ingredients was simply soaring demand, not contraction of supply.”
Horner, who can be described as a development economist, a pharmaceutical industry researcher and an economic geographer, focuses on the global shift in supply chain dependencies. His research examines how the supply chain map is changing and asks a key question – are there systemic risks associated with this remapping of where key ingredients originate?
“There have been fears about risks because of the shift but what bigger test could there have been than the pandemic?” he asks. “And those risks, in many ways, have not materialised in the worst-case scenario that was presented. People feared that China would not cooperate. Policymakers do feel like a different model is needed, but that could have an opportunity cost. It could be difficult to get the funding for domestic production, and drugs could become more expensive.”
One remarkable feature of the pandemic has been the level of vaccine nationalism. Understandably, there has been quicker access to vaccines in domestic markets where vaccine production happens, but this has led some regions, notably Africa, short of supply and forced them to consider local production, which may not be optimal.
“There are advocates of a more localised model and the pandemic shows some nationalist approaches,” says Horner. “In Africa, local production is not the most efficient approach in the short term, as the cost to import is lower, though African countries may want to pursue more health security in the long term. That said, most policymakers are not operating in the long term and are more focused on addressing short-term needs.”
“If the geographic organisation of the industry changes, then someone needs to pay the bill,” he adds. “Currently, the model of globalisation relies on generally lower trade barriers and the market-led organisation of the industry.”
For Horner, the fearmongering around China has, so far, proven to be misplaced. Propaganda on both sides seems to exacerbate the perception problem, but a clearer picture has emerged during the pandemic.
“Fears of a supply chain breakdown came from political concerns, nationalism and barriers on exports,” he remarks. “For instance, in March 2020 India tried to ban the export of certain APIs before diplomatic pressure saw the ban rescinded.”
“A Chinese colleague of mine frequently points out the fear of China in the Western media, but notes that China also needs drugs from elsewhere, including the US and Europe, particularly patented drugs, so there is interdependence in the pharma supply chain,” he adds. “This is a global problem that needs a global response. No one can be completely self-reliant.”
Rethink risk
For Foster, diversification is key to mitigating the risks that might emerge from the remapping of the global supply chain. McKinsey’s research suggests that between 38% and 60% of the international pharma trade, worth between $236bn and $377bn in 2018, could be considered for sourcing diversification.
“Companies can reduce their exposure to single sources and other supply chain risks by diversifying where they buy materials, reverting to domestic production, nearshoring the supply, or offshoring to new locations,” Foster explains. “For pharma companies, relocations are often driven by non-economic factors, such as governments’ desire to bolster national security and become more self-sufficient.”
“Business leaders are at a pivotal moment to not just fix their supply chains with makeshift solutions, but to reimagine them end-to-end,” she adds. “Successful companies will redesign their operations and their supply chains to protect their business against a wider and more acute range of potential shocks and disruptive events. To win in the next-normal environment, companies will need to achieve resilience without unsustainable increases in their costs.”
If, as Horner suggests, the dangers of global shifts have been overplayed, then where are the big risks? Pharmaceutical companies are somewhat more insulated from supply chain shocks than other industries because they hold higher inventory levels, but many risks remain. For instance, cyberattacks such as that suffered by Merck in 2017 can cause significant losses in revenue and disrupt supply chains.
“To thrive in a volatile and unpredictable post-pandemic economy, companies will need multiple levers to achieve the operational resilience needed to ride out shocks and disruptions, and the agility to exploit emerging opportunities,” says Foster.
“A lack of visibility into the business practices of suppliers and suppliers’ suppliers can also be a significant risk for pharma companies,” she adds. “It is vital to have a clear understanding of exposures beyond inventory levels, including how products are developed, delivered, and stored, because each stage poses its own potential problems.”
Lessons for the future
Pharmaceutical supply chains have historically been less automated than in other industries, so there is scope for technology to improve resilience. Digitalisation will play a key role in providing visibility into suppliers’ businesses, for example, and could help to boost cybersecurity.
“Converging factors are fuelling a technology revolution for pharma operations, including the use of advanced technologies such as digital analytics that can not only improve a company’s risk management, but deliver a step change in performance in the long term,” Foster believes.
“Successful supply chain risk management starts with getting a clear picture of what’s happening at each phase of production – from sourcing of raw materials to final delivery – which requires gathering internal and external data sources in seven key areas: data security, finance, operations, organisational maturity, regulation, reputation, and structure,” she adds.
For Horner, recent supply chain failures have been caused largely by the rapid scaling up of production to meet increased demand, which has focused attention on increasing efficiency, but much depends on policymakers, whose constituents are now more likely to vote on the issue of health security.
“The problem needs a long-term approach,” he remarks. “Ultimately, the solutions lie in policy coordination. One option is digital technology that brings jobs and pharma production back on shore, but I don’t see that being sufficient. To me, it is about policy coordination to ensure the supply of ingredients.”
There is no single magic bullet that will improve the resilience of the pharmaceutical supply chain, but there are many levers that can be pulled to manage the complexity and adapt to the new normal. While technology will play a role, collaboration between countries and supply chain partners will be the most important factor. Global risks require, after all, a global response.
$629bn
The worldwide value of pharmaceutical goods has grown sixfold in the past two decades, rising from $113bn in 2000 to this figure in 2019.
$236bn – $377bn
Between 38% and 60% of the international pharma trade could potentially be considered for sourcing diversification.
McKinsey & Company
What about biopharmaceutical supply chains?
The impact of Covid-19 has had a major effect on biopharmaceutical supply chains. Like most other industries, these manufacturers continue to struggle with sourcing raw materials and ensuring the timely delivery of finished goods. Supply chain experts believe these challenges aren’t likely to end anytime soon. Ports in America and around the world continue to deal with record levels of congestion, and labour shortages are hampering the ability of logistics companies to move goods – including vaccines and drugs – over land. Manufacturing disruptions caused by outbreaks of Covid-19 in East Asia may also make the procurement of raw materials and essential product components much more difficult than before the pandemic began.
Resilience has become more important than ever for pharma supply chains. In response to these challenges, biopharmaceutical manufacturers are looking for ways to strengthen their supply chains against ongoing volatility and emerging threats, like cyberattacks. In general, biopharma manufacturers are outsourcing and regionalising more, as well as looking for second sources that can make supply chains more resilient. As a result, companies are coordinating increasingly global and distributed strategies.
In 2022, these new supply chain strategies could become the norm for major manufacturers, especially as businesses continue to struggle with the ongoing impact of Covid-related supply chain challenges.
Source: International Society of Automation