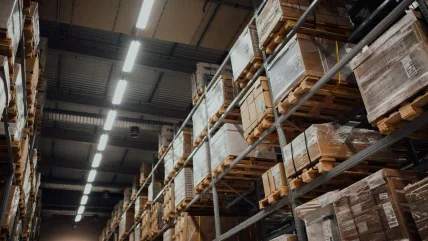
A broken chain can’t function – and, though the supply chain is an alloy unto itself, it still gets brittle when the temperature drops. That’s a problem, because the cold chain is absolutely critical not only to the distribution, but also to the effectiveness and safety of many pharmaceutical products. It must remain intact – that is, within a specified temperature range – from the moment a shipment is ordered right through to arrival at its final destination (which, ultimately, is the patient’s body).
“The importance of the cold chain is to maintain product integrity of temperature-sensitive products throughout the supply chain, from manufacturing to the end user or customer,” explains Brandon Staten, a staff engineer at Janssen supply chain’s Device and Packaging Centre of Excellence. “Considering the wide range of temperature-sensitive products within Janssen’s portfolio, we take this responsibility to maintain our cold chain very seriously.”
In practice, that means doing a lot of risk monitoring and strategic management. The sheer complexity of modern supply lanes means there are countless points along the logistical timeline at which the cold chain can fail. During its journey, a shipment will travel over many different countries, experiencing diverse terrains and a wide range of temperatures. Goods in transit are vulnerable, and the larger and more valuable the shipment, the greater the risk involved. Janssen and other drug companies are effectively rappelling their products down through a labyrinth cut vertically into an Arctic cliff face from a line of A4 sheets stapled end-to-end. It pays to check and check again.
“Janssen ensures success by assessing end-to-end supply chain operations and utilising continuous monitoring to identify potential risks in the storage or distribution environments,” says Staten. “From empirical experience and data, standard operating procedures have been developed and implemented globally. Prioritising customer needs, establishing strong relationships and continuously engaging with external partners, exploring new technologies, auditing and challenging our ways of working, all contribute to robust end-to-end cold chain success.”
Plan and trace
All of those inputs and considerations come together in a strategic risk management plan, which is essential for navigating the perils associated with international distribution. Such a plan will consider all of the points at which things could go wrong in the cold chain process – everything from sudden changes in temperature as goods are moved, and loss or damage to the cargo, to delay or disruption due to incorrect paperwork.
“Understanding and identifying potential temperature risks within the supply chain is one of the initial steps to mitigating risk,” says Staten. Janssen does a good line in that, as he explains. “Storage facilities are temperature-mapped and monitored by calibrated devices. Thermal and physical protections for product storage, handling and distribution, such as passive packaging solutions and active temperature control solutions, are qualified to meet requirements for use. Transportation routes are verified and qualified for logistics prior to product shipments.”
That takes some unpacking, and a specialist cold chain courier or shipment company can help manufacturers analyse and mitigate many of the issues around packaging, temperature monitoring and lane optimisation. Opening good lines of communication and involving such experts early in the planning process means they can select the safest and fastest door-to-door delivery routes, and lessen risk by identifying the most important elements for determining the success or failure of a specific cold chain shipment.
As packaging is often the last line of defence for a temperature-sensitive pharmaceutical, the questions around it are manifold. Yet they can’t be considered separately from those of product value, storage conditions, temperature monitoring and shipping. The decision to use single-use frozen gel packs, reusable solid plastic ice packs, the new generation of phase change materials, or even simple cardboard boxes, comes down to a host of considerations around price, the risk associated with a particular lane or distribution route, the need to be able to reverse the logistics, and much more.
Specialist cold chain vendors and carriers will have expertise in the fastest, safest and most convenient means of moving goods internationally. That’s typically via air, but the most expensive route is not necessarily the most appropriate. Direct, singletrip deliveries mitigate risk – there’s no moving of products between different modes of transport – but as companies have become more mindful of the environmental and economic costs associated with air freight, consignments are often sent by sea.
It’s a complex decision, but adding extra journey time generally introduces greater risk into the cold chain. There’s usually a mitigation strategy, though – at least until there isn’t. Sea freight might simply be unsuitable for some types of delivery – what might be appropriate for temperature-stable commercial drug products probably won’t be right for investigative biologics in late-stage clinical trials, for example.
Not that pharmaceuticals need to be in motion to be at risk. Storage should also be given consideration if products need to be housed in refrigeration units and warehouses before they begin their journey to their destinations, or even once they get there. Continuous and preventative maintenance of cooling units and the provision of suitable backup systems will reduce the risk of malfunction and the consequential deterioration of pharmaceutical products during their journey.
“Understanding and identifying potential temperature risks within the supply chain is one of the initial steps to mitigating risk.”
Brandon Staten
Those costs pile up quickly, which is particularly troubling as decisions over packaging, transport and storage will be made blind if there’s no way to monitor their impact. As great as their investments might be elsewhere, without temperature sensors, companies can’t truly be confident about the security and resilience of their cold chains. Nor can they understand how to improve their processes, lower their risks or optimise their spend. Once you have the right sensors, it’s important they’re positioned correctly to take accurate readings, not only at the beginning and end of the process, but in transit to confirm whether or not there has been any deviation from the specified range – and, just as importantly, how long it might have lasted.
Sensors should also be situated in transport vehicles to detect temperature variations as the shipment traverses different temperature and weather conditions. A good understanding of the temperature stability of a vehicle can help optimise the spend on packaging (and vice versa). Much of the technological development in this space is now focused on integrating these sensors with GPS trackers to monitor consignments and provide automatic scanning and tracking information, as well as real-time updates at each stage of the journey. As such, the latest tracking technology can help companies make live corrections to protect both products and patients.
Finally, a strategic risk management plan should also consider the rules and regulations that apply to carrying goods internationally. Although the EU’s guidelines for good distribution practice (GDP) form the basis of the legislative frameworks in many countries, regulations still vary – sometimes even within the same jurisdiction. That means it’s imperative that pharmaceutical companies select carriers with experience of successfully solving problems and navigating different customs processes to avoid unnecessary delays. This can help decrease costs associated with late or damaged cargo, loss of insurance coverage and payment issues.
While many countries now employ paperless documentation – including import permits, custom documents and taxation information, and health and safety certificates – virtual paperwork is still paperwork: everything still has to be prepared before shipping. It’s necessary to properly document the origin, transportation process and destination of goods to reduce the risk of them being delayed at customs.
Precis it down
You can take a breath now – we’ve reached our destination. Those tricksy variables are all behind us. Now’s the chance to look back and work out how to make managing them a little easier. Janssen does a lot of that, explains Staten, by building on its established cold chain experience, applying proven qualification methods and making data-driven decisions. “Additionally,” he continues, “we routinely partner with academia and suppliers central to the industry to research new technologies that may enhance temperature control in a changing environment.”
As an emerging problem-solving technology, AI and machine learning (ML) could make risk management much less of a human headache. George Baryannis, an expert in AI and service-oriented computing with a particular focus on supply chains, believes pharmaceutical companies can employ AI/ML throughout the risk management process, from initially identifying risks, to assessing their impact and formulating response plans.
“Provided that enough data is available, ML models can be trained to determine whether parts of the supply chain are prone to supply, demand or product risks, or potential disruptions external to the supply chain,” says Baryannis, who is the senior lecturer in AI at the University of Huddersfield. “For cold chains, this could indicatively involve identifying nodes in the supply chain network with the most significant negative effect on the quality of perishable products.”
In terms of risk assessment, probabilistic models such as Bayesian networks (graphical illustrations that, by representing data on the edges of a directed graph, aim to model conditional dependence and thus causation) can be employed to model risk propagation, explaining how different risks depend on and affect one another, Baryannis continues. A significant amount of research has also focused on the problem of optimal supplier selection, building ML classifiers that can rank suppliers based on historical performance and their overall profile.
“AI and ML can also assist in risk-response decision-making, predicting outcomes of candidate risk-response plans,” says Baryannis. “Particularly for the cold chain, this could mean leveraging sensor data to predict the remaining product shelf life in different risk-response scenarios, and choosing the optimal given particular quality or cost thresholds.”
That’s extremely important. The cold chain doesn’t have to be as brittle as it seems today. By mixing in a bit more digitisation, we can allow it to bend further without breaking.
In order to set digital cold chains up for success, though, it’s important to work with specialists who work with and sometimes against the data to pinpoint where things might go wrong, and who are well prepared to deal with any situations as they arise.
The cold chain isn’t just the journey itself – it’s the packaging the product is in, the vehicles transporting it, how the product is disseminated at its final destination, and also how all of that information is recorded, stored and accessed. It’s only when we understand that every change introduces its own variables that emerging technologies such as AI and ML can truly increase the cold chain’s resilience.