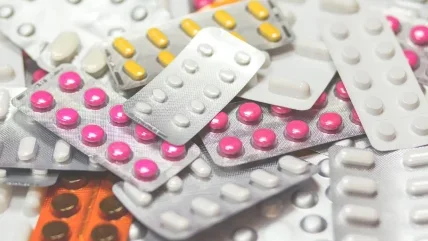
The pharmaceutical industry is no stranger to economic fluctuations, but the recent surge in global inflation presents a unique set of challenges and opportunities. As inflation rates climb, driven by a combination of pandemic-related disruptions, supply chain bottlenecks, and geopolitical tensions, pharmaceutical companies must navigate a complex landscape to maintain stability and growth. This article explores the multifaceted impact of inflation on the pharmaceutical industry, delving into cost pressures, pricing strategies, regulatory responses, and long-term implications.
Understanding inflation in the pharmaceutical context
Inflation refers to the general increase in prices and the corresponding decrease in purchasing power over time. In the pharmaceutical sector, inflation impacts both the cost of production and the pricing of end products. Key factors contributing to inflationary pressures in the industry include:
- Supply Chain Disruptions: The COVID-19 pandemic significantly disrupted global supply chains, affecting the availability of raw materials and active pharmaceutical ingredients (APIs). Ongoing logistics challenges and increased transportation costs have exacerbated these issues.
- Labour Costs: The industry has faced rising labour costs due to increased demand for skilled workers and the necessity to implement stringent health and safety measures. This trend is particularly pronounced in manufacturing and research and development (R&D) sectors.
- Energy Prices: The pharmaceutical manufacturing process is energy-intensive. Rising energy prices, driven by geopolitical factors and market dynamics, have added to the overall cost burden.
Cost pressures and their impact
The pharmaceutical industry is grappling with substantial cost pressures due to inflation. These pressures manifest in several ways:
- Raw Materials and APIs: The prices of raw materials and APIs have surged. For instance, the cost of chemical intermediates has increased due to higher demand and production constraints. This directly affects the cost of drug manufacturing.
- Packaging and Distribution: Inflation has also impacted packaging materials such as glass, plastics, and cardboard. Furthermore, increased fuel prices have led to higher transportation costs, affecting the distribution of pharmaceutical products globally.
- R&D Investments: Inflation can strain budgets allocated for R&D. Pharmaceutical companies must balance the need for innovation with the financial pressures of increased operational costs. This could potentially slow down the development of new drugs and therapies.
Pricing strategies in an inflationary environment
To counteract rising costs, pharmaceutical companies may adopt various pricing strategies. However, these strategies must be carefully managed to avoid negative repercussions such as regulatory scrutiny or public backlash.
- Price Increases: Companies may opt to increase the prices of their products to offset higher costs. While this can help maintain profit margins, it risks making essential medications less affordable for consumers and health systems.
- Product Differentiation: Investing in product differentiation and branding can justify higher prices. By demonstrating superior efficacy, safety, or convenience, companies can position their products as premium offerings.
- Cost Management: Enhancing operational efficiencies and cutting unnecessary expenditures can help mitigate the impact of inflation. Lean manufacturing techniques and supply chain optimisation are critical in this regard.
Regulatory and policy responses
Regulatory bodies and policymakers play a crucial role in shaping the pharmaceutical industry’s response to inflation. Their actions can influence pricing, availability, and innovation.
- Price Controls: In some regions, governments impose price controls on essential medications to ensure affordability. While this protects consumers, it can squeeze profit margins for manufacturers, potentially discouraging investment in new drug development.
- Subsidies and Incentives: To encourage pharmaceutical innovation and mitigate the effects of inflation, governments may offer subsidies or tax incentives for R&D activities. These measures can help offset increased costs and promote continued investment in new therapies.
- International Trade Policies: Changes in international trade policies, such as tariffs and trade agreements, can affect the cost of imported raw materials and APIs. Policymakers must consider the broader implications of these policies on the pharmaceutical supply chain.
Long-term implications and strategic considerations
Inflationary trends have several long-term implications for the pharmaceutical industry, influencing strategic decisions and shaping the future landscape.
- Investment in Localised Production: To reduce dependence on volatile global supply chains, companies may invest in localised production facilities. This strategy can enhance supply chain resilience and reduce exposure to international cost fluctuations.
- Sustainability Initiatives: Embracing sustainability can help manage costs and meet regulatory requirements. For example, investing in energy-efficient technologies and sustainable sourcing practices can mitigate the impact of rising energy prices.
- Collaborative R&D Efforts: Collaborations between pharmaceutical companies, academic institutions, and government agencies can pool resources and expertise, facilitating more cost-effective R&D. Such partnerships are particularly valuable in addressing complex health challenges.
Case studies: industry responses to inflation
Examining how leading pharmaceutical companies have responded to inflationary pressures provides valuable insights into effective strategies and practices.
- Pfizer: In response to rising costs, Pfizer has focused on operational efficiencies and strategic acquisitions to bolster its pipeline. The company’s emphasis on innovative therapies and vaccines has helped maintain strong financial performance despite inflationary challenges.
- Roche: Roche has invested heavily in digital transformation and automation to enhance manufacturing efficiency. By leveraging advanced technologies, the company aims to reduce production costs and improve supply chain resilience.
- AstraZeneca: AstraZeneca has pursued a strategy of diversifying its supply chain and increasing local production capabilities. This approach has helped mitigate the impact of global supply chain disruptions and rising transportation costs.
Conclusion
Inflation presents a complex set of challenges and opportunities for the pharmaceutical industry. By understanding the key drivers of inflation and implementing strategic responses, companies can navigate this turbulent landscape. Effective cost management, innovative pricing strategies, and proactive regulatory engagement are crucial for sustaining growth and ensuring the continued availability of essential medications.
As the industry adapts to these economic pressures, collaboration and innovation will remain at the forefront of its efforts. By embracing these principles, pharmaceutical companies can not only weather the storm of inflation but also emerge stronger and more resilient in the face of future challenges.